_ WHO WE ARE
Worm Drive Clamp Family
Worm Drive Clamp Family
1. How to select a hose clamp?
Selection of clamp based on-
TYPE: Based on your application Light duty, Medium Duty and Heavy duty
SIZE: Hose clamp size refers to the clamping diameter range, depending upon minimum and maximum achievable diameter. To determine the dimensions needed, install the hose on the spigot with bead (which expands over the hose), now measure the maximum diameter of the hose, then select a clamp that accommodates the mean diameter in about the centre of its range.
Ideally clamp should be used up to 25% on either side of mean clamp diameter i.e., if the clamp size is 50-70mm (20mm range, mean diameter- 60mm) the ideal clamping range should be 55-65mm only.
MATERIAL GRADE: Based on the operating environment conditions & material corrosion resistance clamp material grade should be selected.
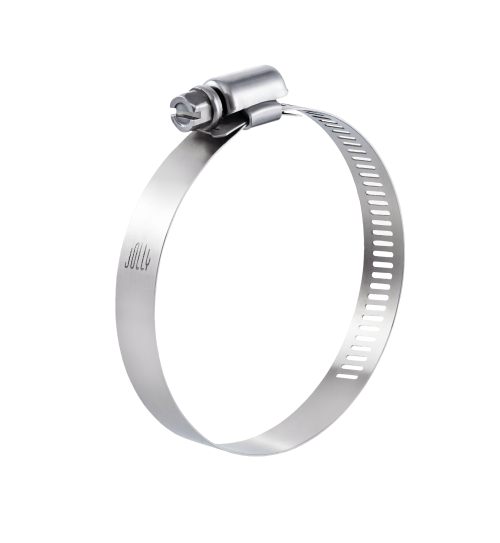
Code | Material | Corrosion Resistance Min. (hrs) |
---|---|---|
W3 | SS430 | 200 |
W4 | SS304 | 400 |
W5 | SS316 | 1000 |
2. Difference between Perforated & Serrated clamps & application basis selection of clamp.
The basic difference between Perforated and Serrated clamps is, Perforated clamps have pierced teeth on the band of the clamp which engages with the screw, whereas in case of Serrated clamps, the teeth on band are formed which engages with the screw to provide the necessary clamping force.
In case of perforated clamps there is a possibility of hose biting on a soft hoses due to pierced teeth. To avoid this liner can be orovided to protect soft hose in the specific application. Application torque in perforated clamps would be higher than serrated clamps.
In serrated clamps hose biting issue doesn’t arise due to rolled edges of the threads and smooth underside. Also, the serrated clamp’s residual torque is higher by almost 30% to 50% than perforated clamp.
Note: Perforated clamps confirms SAE J1508 American standard, while Serrated clamps confirms to DIN 3017 German standard.
3. Why is the use of Hose clamp not suggested
on close diameter?
The bottom radius of the clamp housing is adjusted to mean clamp diameter, so if the clamp is tightened on the close diameter there are enhanced possibilities of joint leakage. Also, if the clamp is tightened on the close diameter there will be a long band protruding out of the clamp which may hinder the operator while maintenance tasks & assembling / dismantling time is also wasted.
4.Difference between Heavy Duty &
conventional clamp
The heavy-duty worm drive clamp has more precise & firm engagement of screw & Band achieved by the use of Split housing construction. Split construction of housing provides better torque retention abilities to the clamp. Rigid split construction allows the clamp to withstand higher application torque.